Ensayos ultrasónicos de la vía férrea: ¿ruedas o patines? ¿Qué elegir?
(Métodos de entrada de ultrasonido en pruebas continuas de rieles - ventajas y desventajas)
Introducción
En actualidad, en los mercados de Europa, América, Australia y otros países, hay docenas de equipos de inspección continua de vías férreas: carros portátiles de una y dos vías, vehículos y vagones de inspección ferroviaria. Casi todos ellos utilizan esquemas tradicionales de entrada de ultrasonido que permiten inspeccionar la cabeza y la sección central del riel:
0°: se utiliza para detectar la delaminación horizontal a lo largo de toda la altura del riel y analizar el acoplamiento acústico (según el nivel de la señal de fondo).
70°: sirve para detectar las grietas transversales en la cabeza del riel, se utilizan sondas orientadas en dirección del movimiento y contraria. En algunas modificaciones del sistema de búsqueda, se utilizan tres elementos piezoeléctricos (ya sea por separado o en una carcasa), garantizando así la prueba de todo el ancho de la cabeza del riel.
35° (38°, 45°): se utilizan para la inspección del alma y la base del riel, tanto con sondas orientadas en dirección y contraria al movimiento.
Para detectar las grietas verticales en las partes laterales de la cabeza del riel, se utiliza el esquema de inspección denominado "Mirada lateral" («Side Looking») con un ángulo de la sonda de 40°/55°.
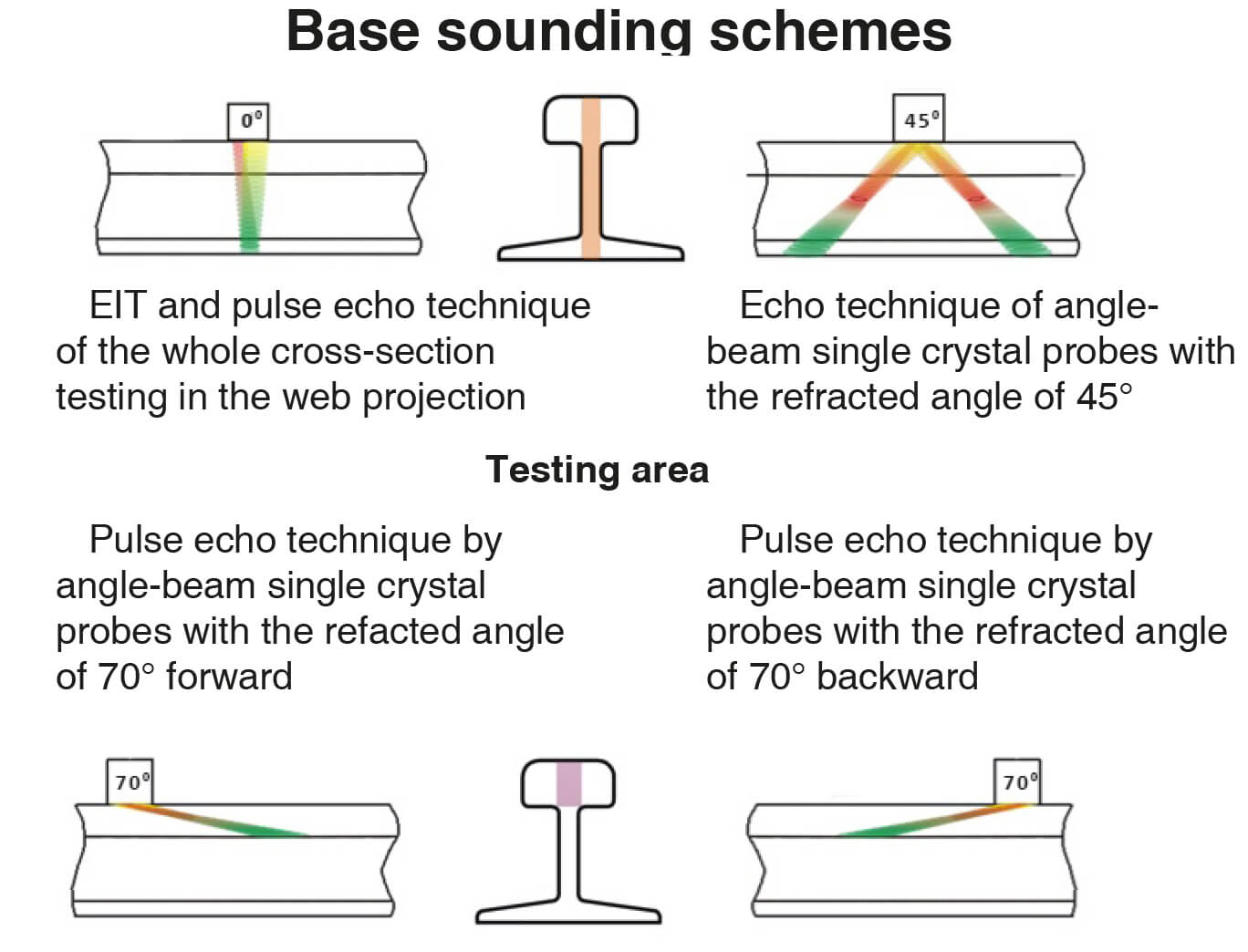
Tipos de sistemas de búsqueda
La colocación de las sondas ultrasónicas y la entrada de ultrasonido se realiza principalmente de dos maneras: "sonda ultrasónica de rueda" (ver Figura 1) y sondas deslizantes ("slides"), que son ampliamente utilizadas en Europa del Este (ver Figura 2);
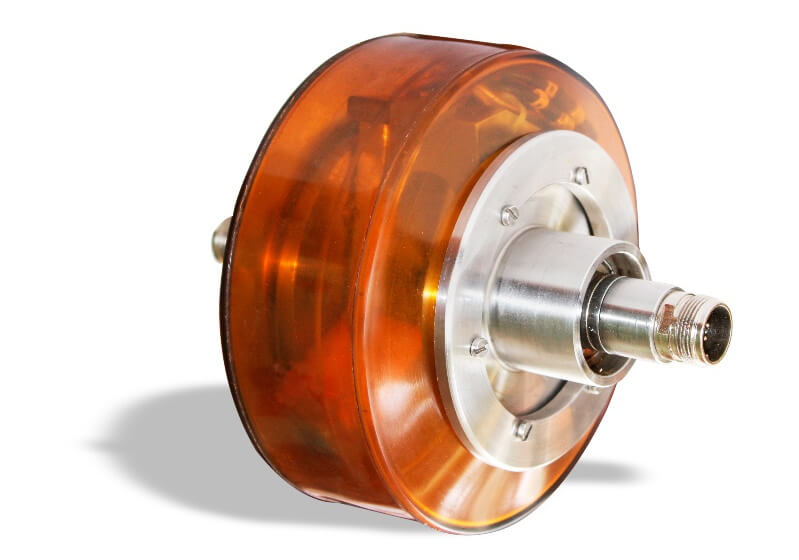
Figura 1 - Sistema ultrasónico de búsqueda de ruedas
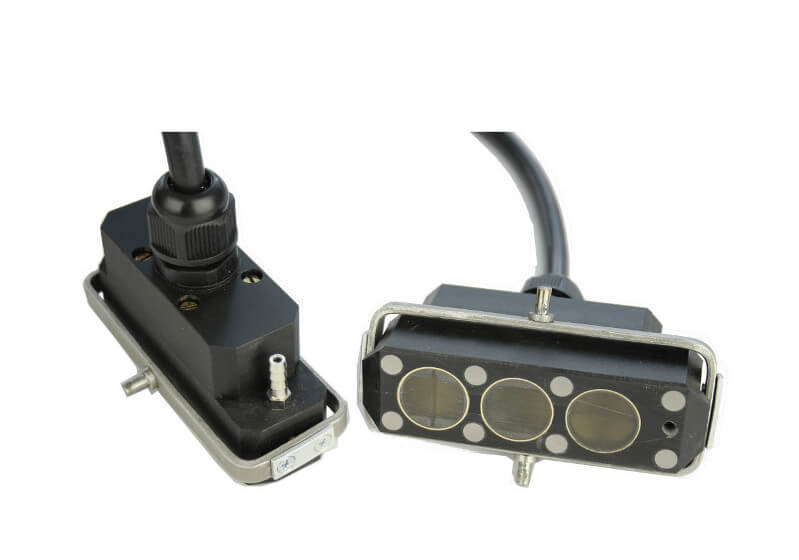
Figura 2 - Unidades acústicas del sistema de búsqueda deslizante
Ventajas y desventajas de los sistemas de entrada de ultrasonido
Sistema deslizante
Para los sistemas deslizantes que se utilizan en vehículos de prueba de alta velocidad, es crucial proporcionar un contacto acústico estable, Esto se logra mediante un sistema de seguimiento automático de la superficie del riel (parte mecánica), así como por un sistema de riego preliminar del riel y por un sistema de suministro de líquido de contacto directamente a las sondas. Para la humectación y limpieza del riel, se utiliza un chorro de agua a alta presión (hasta 100 bares).
A las sondas (bloques acústicos) el líquido de contacto se suministra también bajo cierta presión. En algunos equipos de inspección, el líquido de contacto se suministra en forma dispersa, lo que permite ahorrar su cantidad y mejorar la estabilidad del contacto acústico.
Por lo tanto, para garantizar un contacto acústico estable, el sistema deslizante requiere un alto consumo de líquido (agua), lo cual es una de sus desventajas.
La segunda desventaja del sistema deslizante es el contacto directo de los bloques acústicos con la superficie de rodadura del riel, lo que provoca un desgaste bastante rápido de los bloques del sensor. Para evitar el desgaste de los transductores, se utilizan protectores llamados "zapatos protectores". Estos zapatos protectores suelen estar hechos de vidrio orgánico o poliuretano sólido, y son materiales de consumo.
UDS2-77 - ultrasonic flaw detector for testing
the condition of one rail
Explore More Sistema de búsqueda de rueda
El sistema de búsqueda de rueda representa en realidad una rueda con un neumático de poliuretano en el cual se instalan las sondas ultrasónicas. La rueda está llena de un líquido de inmersión (generalmente se utiliza etilenglicol). El sistema de búsqueda de rueda con ubicación de sondas se muestra en la Figura 3.
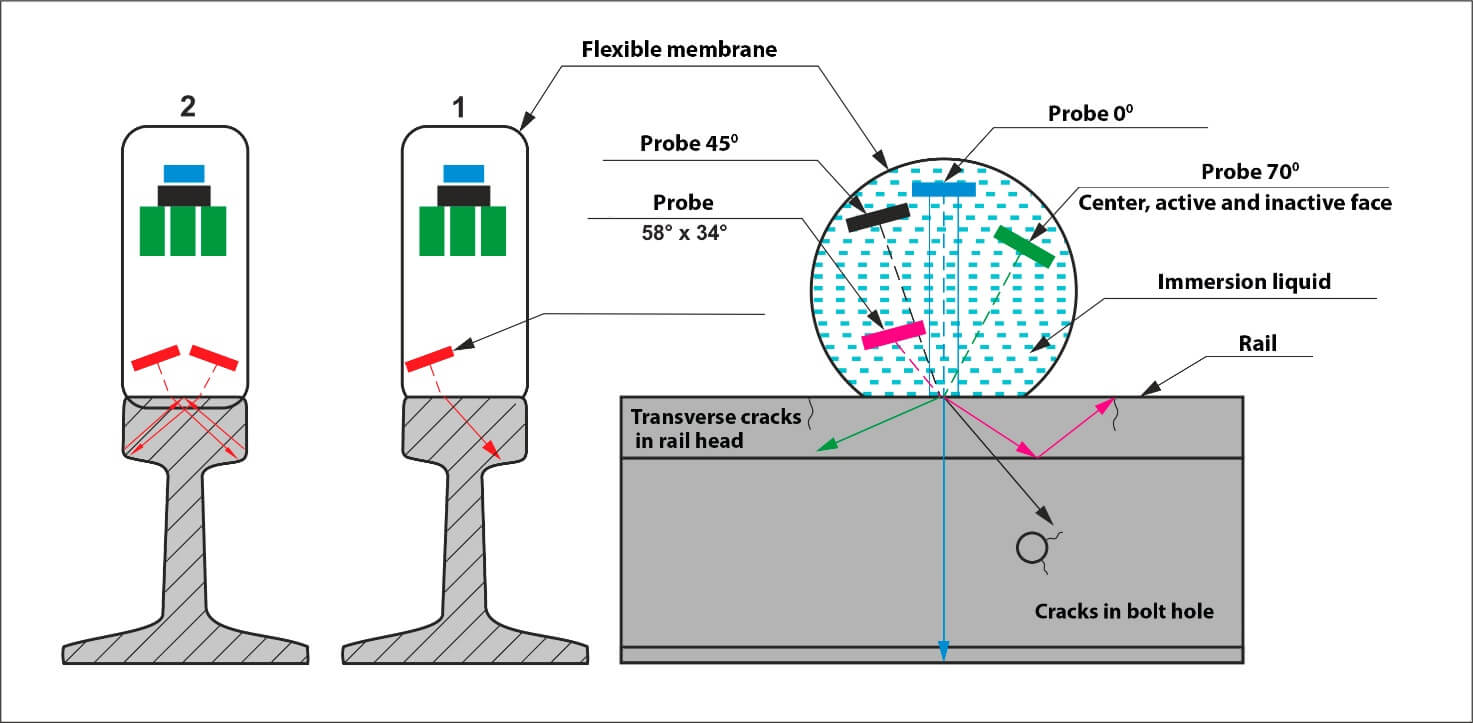
Uno de los beneficios más destacados del sistema de búsqueda de rueda es su neumático elástico que bordea estrechamente la superficie de rodadura de la cabeza del riel incluso si la cabeza del riel está desgastada. Además, al cambiar la presión en la rueda ultrasónica, es posible variar las dimensiones del área de contacto. Esto asegura una mayor estabilidad del acoplamiento acústico y, a su vez, proporciona la posibilidad de probar rieles a una velocidad de hasta 40 km/h. Otra ventaja del sistema de búsqueda de rueda es un consumo mucho menor del líquido de acoplamiento en comparación con el sistema de búsqueda deslizante. Esto se logra gracias al uso del neumático de poliuretano.
Naturalmente, el sistema de búsqueda de rueda, con todas sus ventajas, tiene algunas desventajas. Una de las desventajas esenciales es la necesidad de un ajuste preciso de la posición de la rueda en relación con la superficie del riel en todos los planos. El cambio de orientación en 10 en cualquier plano puede provocar un cambio en el ángulo de entrada de ultrasonido en metal (en el plano respectivo) en 40 y la distorsión del esquema de sondeo. Como resultado, el operador puede omitir incluso defectos bastante grandes. Por eso no se recomienda el uso del sistema de rueda en detectores de fallas para la inspección de un carril. Algunos fabricantes ignoran esta limitación e instalan una barra estabilizadora adicional con la rueda que se apoya sobre el segundo riel, pero en este caso se reduce significativamente la comodidad del uso del dispositivo.
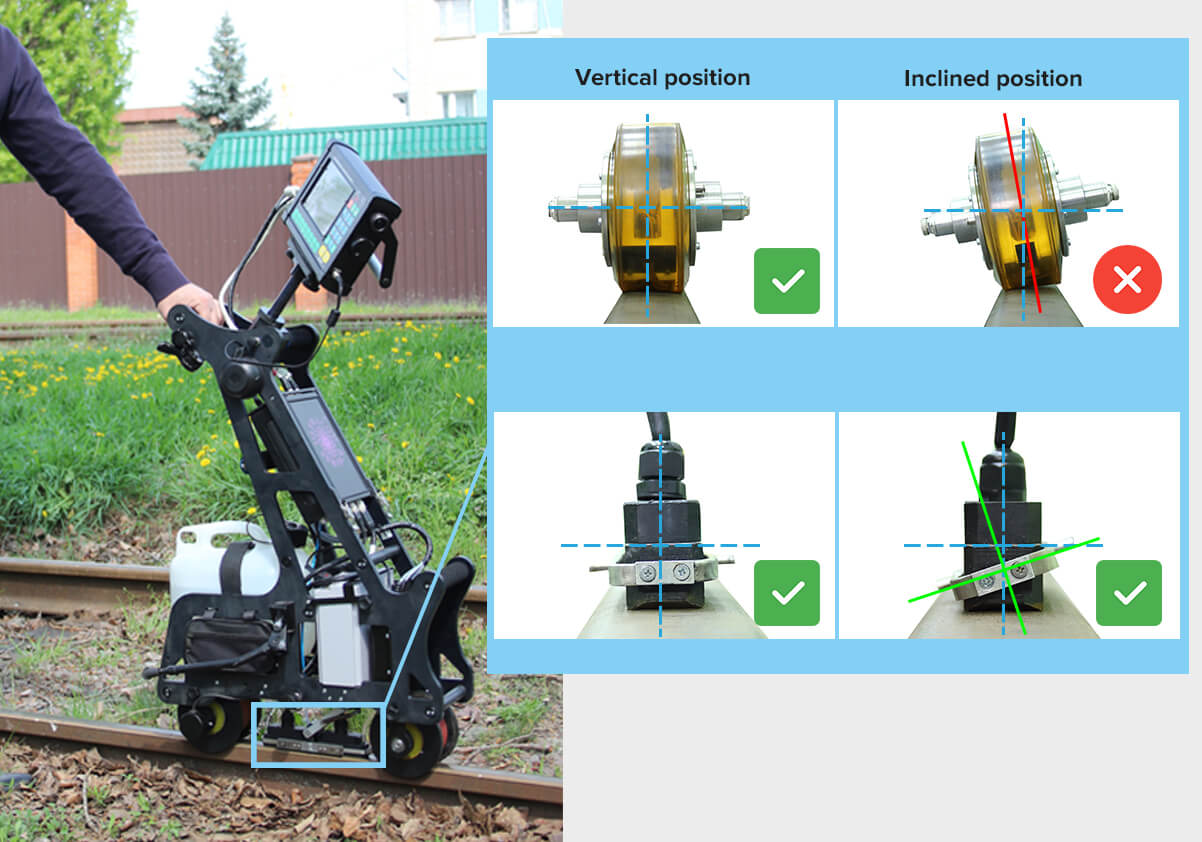
Otra desventaja del sistema de inspección de rueda en comparación con el sistema deslizante es que con el uso del primero es imposible implementar algunos esquemas de inspección, en particular aquellos que requieren una distancia fija entre los transductores (por ejemplo, el esquema "Tandem"). Esto se debe a la geometría de las ruedas ultrasónicas y la imposibilidad de colocarlas a la distancia requerida entre sí. Esta limitación conduce a una menor detección de defectos planos en la cabeza del riel que no afloran a la superficie del riel.
Y finalmente, una desventaja relacionada con la limitación de la velocidad de inspección que surge de los principios del método de inspección por inmersión. En el sistema de ruedas, el tiempo requerido para que las oscilaciones ultrasónicas pasen desde el transductor hasta el borde del neumático es comparable o incluso mayor que el tiempo requerido para que las oscilaciones pasen a través del cuerpo del riel. Como resultado, el tiempo total de vuelo de ultrasonido desde el transmisor a través del líquido de inmersión hasta la superficie inferior del riel y de regreso al receptor es al menos el doble que en un sistema deslizante. Esto impone limitaciones a la frecuencia de los pulsos de inspección y, por lo tanto, a la velocidad de inspección a la cual los defectos necesarios pueden detectarse de manera confiable. En los equipos de inspección que utilizan sistemas de ruedas ultrasónicas, la distancia entre escaneos suele ser aproximadamente de 4 mm. Y la velocidad de inspección puede alcanzar hasta 40 km/h.
En un sistema de búsqueda deslizante, las oscilaciones ultrasónicas se introducen directamente en el objeto de inspección, lo que permite aumentar la frecuencia de los pulsos de inspección al menos en doble, lo que a su vez conduce a un aumento en la velocidad de exploración o a una reducción en el paso de inspección. Por ejemplo, a la misma velocidad de exploración de 40 km/h, el paso de inspección al utilizar un sistema de inspección deslizante sería de 2 mm.
Conclusión
Cada uno de los sistemas de inspección descritos puede utilizarse para la inspección continua de vías férreas, y cada uno tiene sus pros y sus contras. Por lo tanto, la elección de los tipos de sistemas de búsqueda depende principalmente de la tradición de una empresa de servicios ferroviarios. Por lo tanto, OKOndt GROUP fabrica y mejora constantemente ambos tipos de sistemas de inspección, tanto deslizantes como de ruedas.