La inspección manual de carriles en la vía férrea se utiliza en dos casos:
- Para la inspección de confirmación de los defectos detectados durante la inspección continua de carriles con detectores de fallas de uno o dos carriles o, en algunos casos, con sistemas de inspección de carriles por ultrasonidos de alta velocidad.
- Para la inspección de aceptación de juntas de soldaduras aluminotérmicas de rieles.
Introducción
La inspección manual de carriles en la vía férrea se utiliza en dos casos:
- Para la inspección de confirmación de los defectos detectados durante la inspección continua de carriles con detectores de fallas de uno o dos carriles o, en algunos casos, con sistemas de inspección de carriles por ultrasonidos de alta velocidad.
- Para la inspección de aceptación de juntas de soldaduras aluminotérmicas de rieles.
Examinemos cada una de estas aplicaciones por separado.
Inspección de confirmación para verificar los resultados de la inspección continua
De forma similar a la inspección continua, las inspecciones manuales con detectores de fallas portátiles se realizan de acuerdo con los esquemas de sondeo descritos en la norma EN 16729-1 y los documentos normativos relacionados.
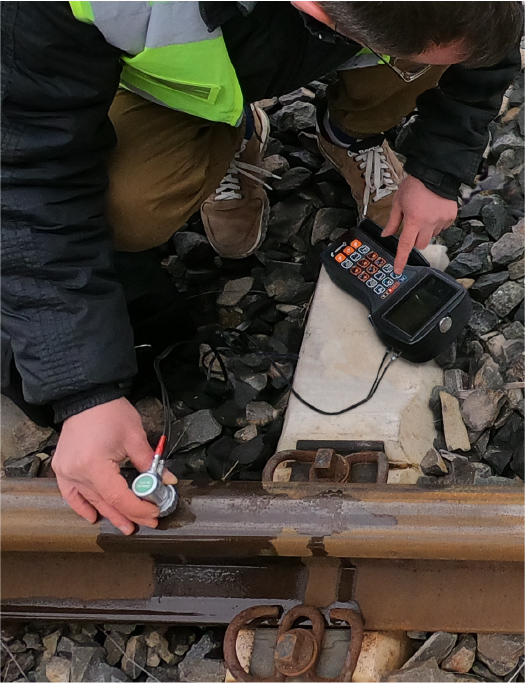
Los defectos que se detectan con mayor frecuencia son los de la cabeza de riel, principalmente grietas transversales (incluido head checks en la cabeza). Para detectar estos defectos se suelen utilizar transductores de elemento único de haz angular de unos 70°, de elemento único con frecuencias de 2-2,5 MHz. La necesidad de hacer una inspección de confirmación puede ser determinada por varios factores:
- primero: en rieles con un desgaste importante de la superficie de trabajo, los sensores de 70°, que inspeccionan la zona de la región esquina de trocha de la cabeza del riel en sistemas de prueba continua, pueden experimentar un acoplamiento acústico inestable y presentar una serie de señales falsas causadas por reflexiones ultrasónicas repetidas dentro de la capa de líquido de acoplamiento engrosada.
- segundo: en algunos casos, es necesario aclarar la localización del defecto y su aceptabilidad. Por ejemplo, cuando los defectos detectados durante la inspección continua muestran amplitudes cercanas al umbral de detección. A diferencia de la inspección continua, la inspección manual de la cabeza del carril permite sondear los defectos no sólo «a lo largo del carril», sino también inclinando los transductores en varios ángulos. Los defectos también pueden comprobarse desde las superficies laterales de la cabeza del riel.
Otros tipos de defectos que a veces requieren una inspección de confirmación son los defectos horizontales, como las delaminaciones y las grietas horizontales. Estos defectos se detectan utilizando un transductor de doble elemento de haz recto con frecuencias de 2-5 MHz (lo más habitual es de 4-5 MHz). Estos transductores tienen una zona cercana muerta mínima (sólo unos milímetros) y pueden inspeccionar toda la sección central del riel hasta e patín. De esta manera se puede también detectar grietas horizontales (o casi horizontales) en orificios de pernos, transiciones del alma a la cabeza y la base, y corrosión del patín mediante cambios de la posición de la señal inferior.
Los daños por corrosión en el patín que conducen al desarrollo de grietas transversales verticales también pueden identificarse utilizando transductores de haz angular de elemento único con ángulos de 35°-45° y frecuencias de 2-2,5 MHz. Estos transductores también pueden detectar grietas en estrella en los orificios de los pernos.
Inspección de juntas soldadas aluminotérmicas
La inspección ultrasónica de aceptación de las juntas soldadas aluminotérmicas de los rieles se regula por la norma EN 14730 y los documentos relacionados. El alcance de la inspección ultrasónica requerida varía significativamente según diferentes ediciones de la norma. En este artículo nosotros examinemos el variante más completo de esquemas de sondeo:
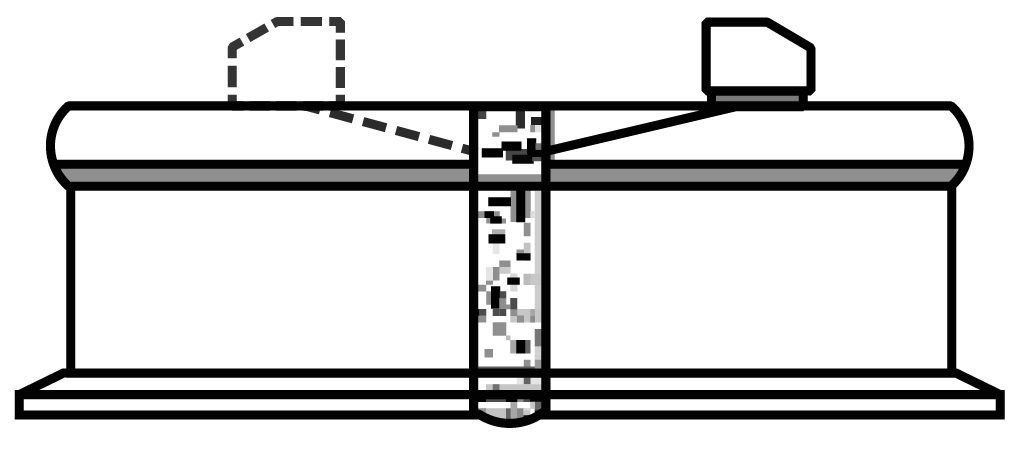
1. Para la inspección de la cabeza del riel se utilizan dos esquemas de sondeo para detectar individualmente defectos volumétricos y planares.
- Defectos volumétricos se detectan utilizando un transductor de haz angular de un solo elemento con un ángulo de 70° y una frecuencia de 2 MHz, escaneando desde la superficie de rodadura a ambos lados de la soldadura.
- Defectos planares se detectan con dos transductores de haz angular de un solo elemento con un ángulo de 70° y una frecuencia de 2 MHz. Estos transductores se colocan mediante un escáner especial en las superficies laterales de la cabeza del raíl, actuando uno como emisor y el otro como receptor. Los transductores se mueven en direcciones opuestas durante la inspección (uno se acerca a la soldadura mientras el otro se aleja), desplazando la zona de inspección hacia el transductor que se acerca a la soldadura.
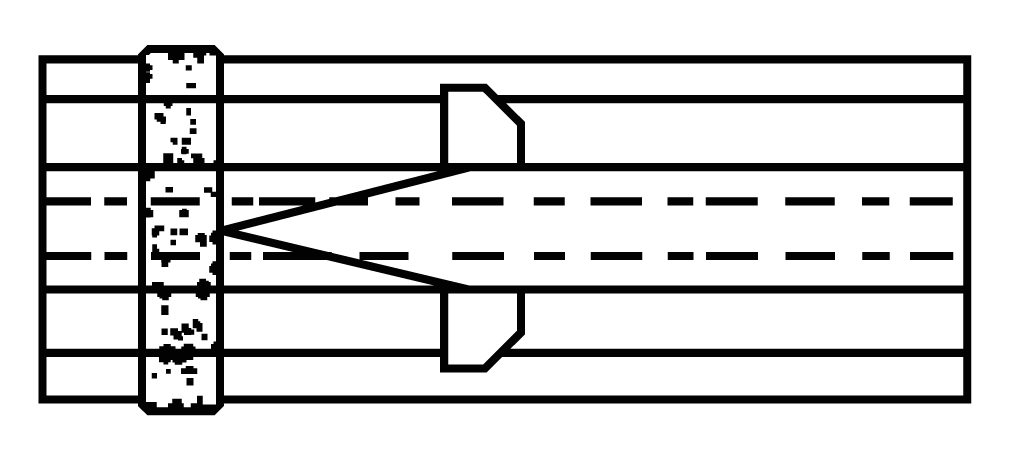
2. La parte central de la cabeza y el alma se inspeccionan principalmente para detectar defectos planares utilizando dos transductores de un solo elemento con un ángulo de 45° y una frecuencia de 2 MHz, colocados en la superficie de rodadura mediante un escáner especial formando un esquema «Tándem». Cuando los transductores convergen, la zona de inspección se desplaza hacia la parte inferior de la soldadura; cuando divergen, se desplaza hacia la parte superior.
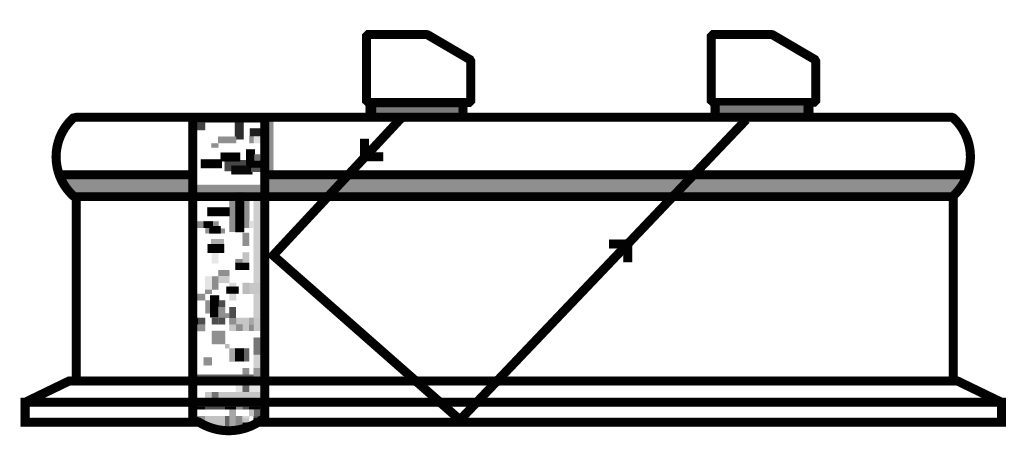
3. La parte central del patín inspeccionan con un transductor de un solo elemento con un ángulo de 45° y una frecuencia de 2 MHz, escaneando a lo largo de la parte central de la superficie de rodadura del carril desde ambos lados de la soldadura.
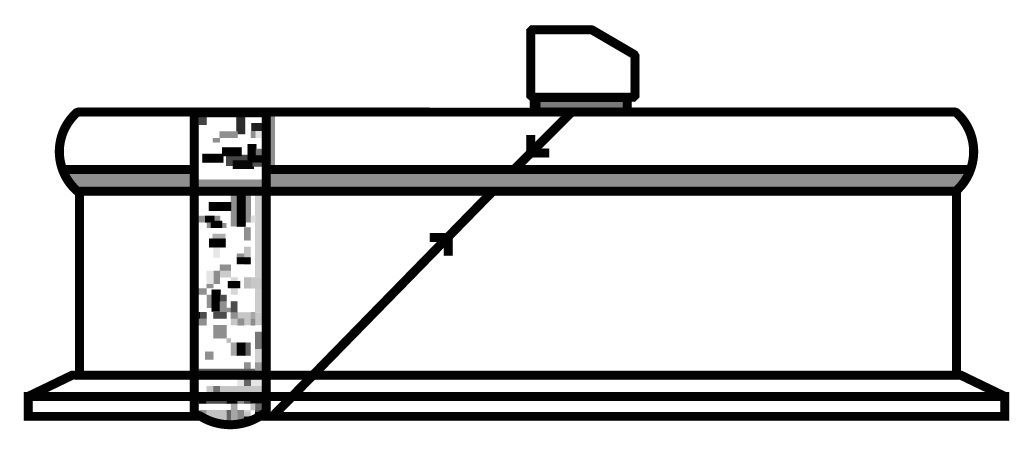
4. Las pestañas del patín inspeccionan con un transductor angular combinado con un ángulo de entrada de 70° y una frecuencia de 2 MHz, escaneando las partes correspondientes de la superficie superior de las pestañas del patín.
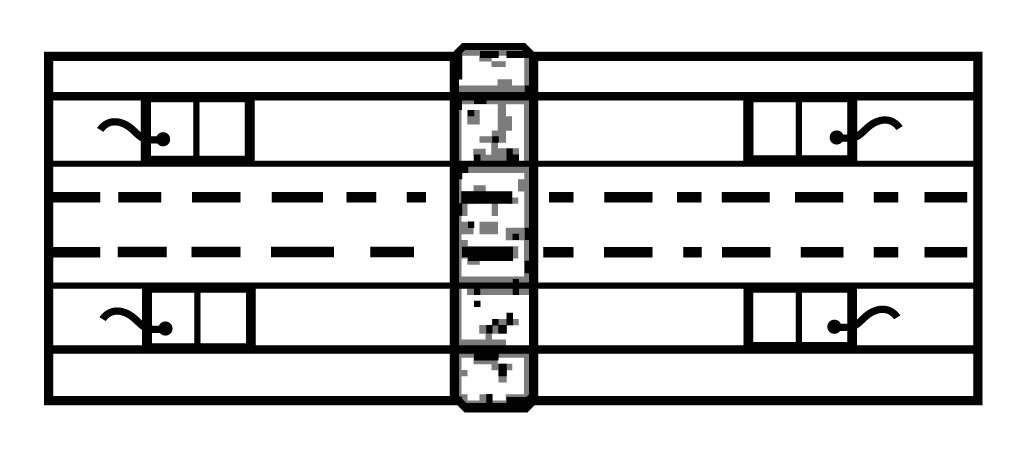
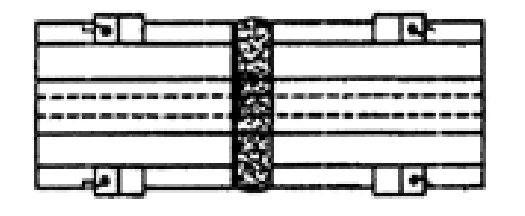
En otra edición de la norma, se regula la inspección por ultrasonidos de las soldaduras aluminotérmicas que deben ser cortadas. En este caso una muestra con unión soldada se cortan a una longitud de 180-230 mm a lo largo del eje del carril (dependiendo de la anchura nominal de la separación). La prueba se realiza con un transductor de doble elemento de haz recto con una frecuencia de 4-5 MHz y un diámetro de 20 mm. La inspección se realiza desde cualquiera de las superficies extremas de la muestra a lo largo de toda el área de la sección del riel mediante técnicas de pulso-eco y eco imágenes.
Equipos para la inspección manual de carriles por ultrasonidos
Algunos detectores de fallas de rieles para la inspección continua, como el UDS2-73 y el UDS2-77, permiten al operador cambiar al modo de inspección manual y utilizar un transductor manual adecuado para las pruebas de confirmación. Sin embargo, los detectores de defectos manuales, como Sonocon B y Sonocon BL, son más convenientes para esta aplicación. Aquí se puede encontrar más detalles sobre sus características, que hacen que su uso sea cómodo y eficaz..