Zerstörungsfreie Prüfung von Schweißverbindungen
Visuelle Prüfung
Kapillarprüfung
Ultraschalluntersuchung
Pulsecho-Methode
Echo-Spiegelungsprüfung
Spiegel-Schatten-Prüfung
TOFD-Prüfung
Wirbelstromprüfung
Magnetpulverprüfung
Röntgenprüfung
Schweißnähte sind in allen Bereichen der industriellen Produktion die häufigste Art von dauerhaften Verbindungen. Es gibt eine große Anzahl ihrer Typen, sowohl von verschiedenen Ausführungsmethoden (manueller Lichtbogen, automatisch und halbautomatisch, untergetauchter Lichtbogen, Lichtbogen in Schutzgas, Kontakt usw.) als auch von den Arten der Verbindungen (Stoß, Winkel, T-Stück, Überlappung). In übrigens, bei jeder Methode die Schweißverbindung wird nach dem Schweißen in den meisten Fällen die Schweißnaht überprüft. Die Fehlererkennung zielt darauf ab, verschiedene Fehler zu identifizieren, die zu einer Schwächung der Festigkeit und Zuverlässigkeit der Verbindung sowie zu einer Verletzung ihrer Dichtheit führen. Die rechtzeitige Erkennung solcher Defekte beeinflusst die Bestimmung der Lebensdauer der Schweißkonstruktion insgesamt erheblich. Die Qualität von Schweißnähten ist besonders wichtig für den Betrieb von Hochdrucksystemen und Behältern, Elemente tragender Strukturen.
Die zerstörungsfreie Prüfung (ZfP) ist die Hauptprüfungsmethode für Schweißverbindungen, da damit die Integrität der gesteuerten Einheit und ihre Leistung erhalten werden können. Es gibt viele ZfP-Methoden und eine große Anzahl von Gerätemodellen, die auf der einen oder anderen Methode basieren. Bei der Auswahl einer Prüfmethode müssen zahlreiche Faktoren berücksichtigt werden, wie z. B. das Material der Schweißteile, die Konstruktion der Schweißverbindung, der Oberflächenzustand, die Qualitätsanforderungen, der Zugang, die Art und der Ort eines möglichen Defekts (Diskontinuität), die Kosten und die Produktivität der Prüfung. In dieser Hinsicht gibt es keine universelle Kontrollmethode, und die Qualität, Zuverlässigkeit und Haltbarkeit des Endprodukts hängt weitgehend von der Wahl der optimalsten Option ab.
Visuelle Prüfung
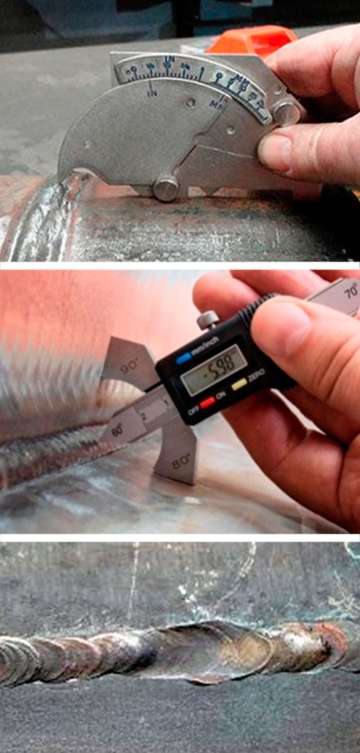
Diese Methode kombiniert die Sichtprüfung und Messung der geometrischen Parameter der getesteten Schweißverbindung, um die Einhaltung der Anforderungen zu überprüfen. Vor der Fehlererkennung sollten die Schweißnähte von Zunder, Metallspritzern und Schlacke gereinigt werden. Danach wird die Oberfläche mit Alkohol behandelt oder mit einer 10% igen Salpetersäurelösung geätzt. Als Werkzeuge für diese Art der Steuerung werden üblicherweise eine Lupe mit 5- oder 10-facher Vergrößerung, Beleuchtungsvorrichtungen sowie Messinstrumente (Lineal, Messschieber, Schablonen) verwendet, mit denen sowohl die Abmessungen der Naht selbst als auch die Abmessungen der erkannten Defekte gesteuert werden ... Trotz ihrer scheinbaren Einfachheit ist diese Art der Steuerung sehr effektiv und geht anderen Steuerungsmethoden voraus. Wenn in diesem Stadium Mängel festgestellt werden, gilt die Naht als zurückgewiesen und nachfolgende Kontrollarten werden nicht mehr durchgeführt. Der offensichtliche Nachteil dieser Methode ist die Unmöglichkeit, die meisten versteckten Mängel zu erkennen, und die Subjektivität der Bewertungsmethoden, was viel Erfahrung des zuständigen Spezialisten erfordert.
Kapillarprüfung
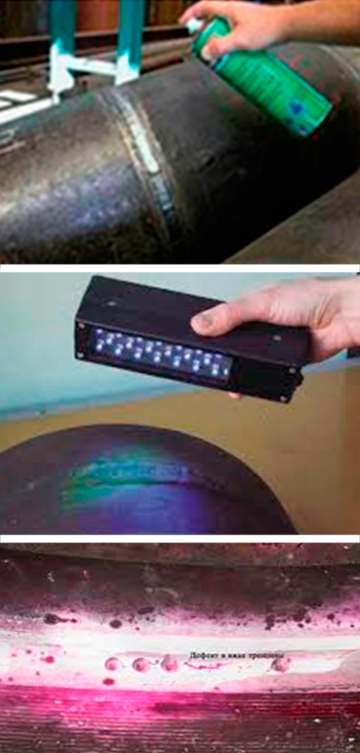
Diese Methode basiert auf der Fähigkeit der Flüssigkeit, in die kleinsten Kanäle einzudringen und diese zu füllen. Im Kern sind diese winzigen Defekte in der Schweißnaht Kapillaren. Dazu gehören beispielsweise Poren und Risse, die auf der Oberfläche des Materials enthalten sind. Die Geschwindigkeit und Tiefe des Eindringens der Flüssigkeit hängt vom Radius der Kapillare und der Benetzbarkeit der Flüssigkeit ab. Somit ist das Kapillarverfahren zum Erkennen von Oberflächendefekten sehr effektiv. Zur Steigerung der Effizienz werden sogenannte Penetrationsmittel eingesetzt, die eine geringe Oberflächenspannung aufweisen und tief in die Kapillare eindringen können. Und ihre helle Farbe macht sie sichtbar, was es einfacher macht, den Defekt zu erkennen. Ein Kapillarprüfungssatz enthält normalerweise: ein Eindringmittel; einen Reiniger, der für eine gründliche Reinigung der Oberfläche vor dem Testen erforderlich ist; ein Entwickler, durch den das Eindringmittel aus dem Defekt entfernt wird und ein Indikatormuster auf einem kontrastierenden Hintergrund erzeugt, anhand dessen man die Größe und Form des Defekts klar beurteilen kann.
Diese Art der Steuerung ist in ihrer Methode der visuellen nahe, da sie durch Untersuchen der Schweißnaht durchgeführt wird und daher die gleichen Nachteile aufweist.
Ultraschalluntersuchung
Die Ultraschallprüfung ist eine der häufigsten Arten von Tests, da damit versteckte Fehler in der Schweißnaht mit hoher Genauigkeit erkannt werden können. Das Verfahren basiert auf der Verwendung von Ultraschallwellen, die die Metallschicht passieren und von ihrer Grenze und den Grenzen der inneren Diskontinuitäten reflektiert werden. Anhand der Zeitdifferenz zwischen den gesendeten und reflektierten Signalen sowie an der Form und Amplitude der reflektierten Signale kann man nicht nur die Dicke des Metalls beurteilen, sondern auch die Defekte, die im Weg des Ultraschallsignals auftreten. Ein Instrument zur Durchführung zerstörungsfreier Ultraschallprüfungen wird als Fehlerdetektor bezeichnet. Der Fehlerdetektor verwendet spezielle Wandler (Sender - Empfänger des Ultraschallsignals), die es ermöglichen, Testmethoden wie Impulsecho, Spiegelecho und Spiegelschatten zu implementieren.
OKOndt GROUP™ produziert verschiedene Ultraschallschweißgeräte. Neben mehreren tragbaren Fehlersuchgeräten haben wir ein spezielles Produkt für die manuelle Prüfung von Schweißverbindungen — USR-01 + Sonocon B .
Pulsecho-Methode
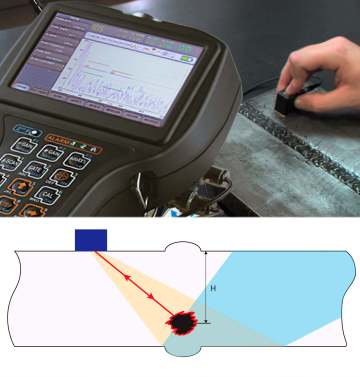
Bei der Impulsechomethode sendet der Wandler ein Sondensignal an das Objekt und empfängt Echosignale, die von Fehlern und Konstruktionsmerkmalen des Produkts reflektiert werden. Die Zeit ihrer Ankunft ermöglicht es uns, die Koordinaten und die Amplitude zu bestimmen - um die Größe der Defekte abzuschätzen. Der Nachteil dieses Verfahrens besteht darin, dass die reflektierende Oberfläche des Defekts senkrecht zum Ultraschallstrahl sein muss oder sich der Defekt nahe der Oberfläche des Produkts befindet. Beispielsweise ermöglicht das Impulsecho-Verfahren nicht das Erkennen von ebenen Defekten (Risse und fehlende Verschmelzung), die nicht nahe an die Oberflächen des Produkts passen.
Echo-Spiegelungsmethode
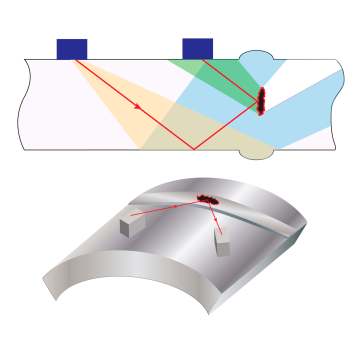
Im Gegenteil, Echospiegelmethoden werden verwendet, um planare Defekte (Risse und fehlende Verschmelzung) zu erkennen - Tandem und Duett. Diese Verfahren verwenden ein Paar von Wandlern, die so installiert sind, dass das vom ersten Wandler emittierte Signal, nachdem es vom ebenen Defekt reflektiert wurde, zum zweiten Wandler zurückkehrt.
Spiegel-Schatten-Methode
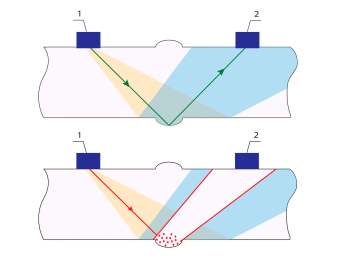
Selbst diese Methode garantiert jedoch nicht die Erkennung von Fehlern in allen Ausrichtungen. Hierzu wird die Spiegelschattenmethode verwendet. Bei Tests nach dieser Methode werden die Sensoren auf beiden Seiten der Naht so installiert, dass das von der Rückseite reflektierte Signal auf den Empfänger trifft. Ausreichend große Defekte praktisch jeder Ausrichtung, die den Ultraschallstrahl kreuzen, verdecken das erwähnte Signal, das ihre Erkennung signalisiert. Diese Methode liefert jedoch leider keine genauen Informationen über die Koordinaten der erkannten Fehler. Um genaue Werte von einem Ultraschall-Fehlerdetektor zu erhalten, muss dieser zunächst mit speziellen Ausrichtungsproben konfiguriert werden, die mit dem Fehlerdetektor geliefert werden.
TOFD – Methode
In den letzten Jahrzehnten hat sich das Zeitbereichsbeugungsverfahren (TOFD) zur Ultraschallprüfung von Schweißnähten weiter verbreitet. TOFD basiert auf der Wechselwirkung von Ultraschallwellen mit den Kanten von Diskontinuitäten. Diese Wechselwirkung führt zur Emission von Beugungswellen über einen weiten Winkelbereich. Die Erfassung von Beugungswellen ermöglicht es, das Vorhandensein einer Diskontinuität festzustellen. Die Laufzeit der aufgezeichneten Signale ist ein Maß für die Schätzung der Höhe der Diskontinuität, wodurch es möglich wird, den Defekt zu messen, und die Größe der Diskontinuität wird immer durch die Laufzeit der Beugungssignale bestimmt. Die Signalamplitude wird nicht zur Dimensionierung verwendet. Darüber hinaus werden sowohl Längs- als auch Querwellen emittiert und angelegt. Das Hauptinformationsmerkmal ist die Ankunftszeit des Signals. Das TOFD-Verfahren hat gegenüber herkömmlichen manuellen Ultraschallverfahren mehrere Vorteile:
- Mehrfach produktiver;
- Etwas empfindlich gegenüber der Ausrichtung von Fehlern;
- Ermöglicht nicht das Abschätzen, sondern das Messen der tatsächlichen Abmessungen von ebenen Defekten;
- Hohe Dokumentierbarkeit der Prüfungsergebnisse.
Zur Implementierung der TOFD-Methode wird eine spezielle Ausrüstung verwendet, bei der ein oder mehrere Doppelandler verwendet werden, die auf beiden Seiten der Naht angeordnet sind und während der Prüfung entlang dieser bewegt werden.
Wirbelstromprüfung
Die zerstörungsfreie Wirbelstromprüfung basiert auf der Analyse der Wechselwirkung eines externen elektromagnetischen Feldes mit dem elektromagnetischen Feld von Wirbelströmen, die im Prüfungsgegenstand durch dieses Feld induziert werden. Das Funktionsprinzip von Wirbelstrom-Fehlerdetektoren besteht darin, Wirbelströme in der lokalen Überwachungszone zu stören und Änderungen des elektromagnetischen Feldes von Wirbelströmen zu registrieren, die durch einen Defekt und die elektrophysikalischen Eigenschaften des Prüflings verursacht werden. Es zeichnet sich durch eine geringe Kontrolltiefe aus. Es wird verwendet, um Risse und Materialdiskontinuitäten in einer Tiefe von 2 mm zu erkennen. Die Entwurfs- und Abstimmungsmethoden von Wirbelstromprüfgeräten ähneln den Entwurfs- und Abstimmungsmethoden ihrer Ultraschallgegenstücke, sie verwenden Wirbelstromwandler bzw. Wirbelstrom-Standardproben. Offensichtlich, ergänzen sich Ultraschall- und Wirbelstromregelungsmethoden und die Vollständigkeit und Zuverlässigkeit der Prüfung der Schweißnaht über ihre gesamte Tiefe und Länge sicherstellen. Geräte zur zerstörungsfreien Wirbelstromprüfung von Schweißnähten werden von OKOndt GROUP in Form verschiedener Modelle von Fehlerdetektoren hergestellt.
Magnetpulverprüfung
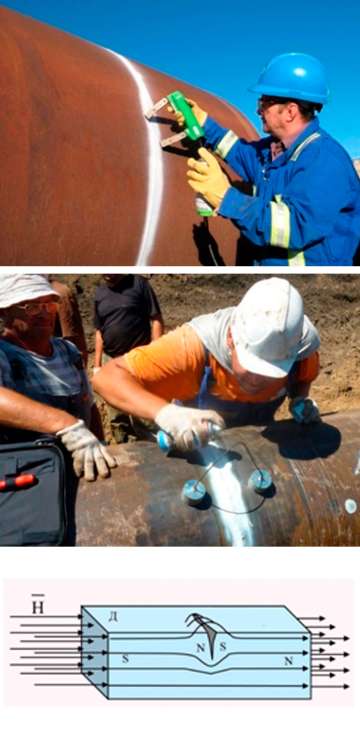
Die Magnetpulverprüfung (MPP) oder die Magnetpulverfehlererkennung (MPF) ist eine zerstörungsfreie Prüfmethode, die auf dem Phänomen der Anziehung magnetischer Pulverteilchen durch magnetische Streuflüsse basiert, die über Defekten in magnetisierten Prüfobjekten auftreten.
Die Magnetpartikelmethode wurde entwickelt, um Oberflächen- und Untergrunddiskontinuitäten wie Haaransatz, Risse verschiedener Herkunft, fehlende Verschmelzung von Schweißverbindungen, Spänen, Sonnenuntergängen, Fehlern usw. zu erkennen. Mit dem Magnetpartikelfehlerdetektor können Teile verschiedener Formen, Schweißnähte und Innenflächen von Löchern geprüft werden, wobei einzelne kontrollierte Bereiche oder das gesamte Produkt mit einem kreisförmigen oder longitudinalen Feld magnetisiert werden, das mit einer Reihe von Magnetisierungsgeräten erzeugt wird, die mit einem Impuls- oder Gleichstrom betrieben werden, oder mit Permanentmagneten.
Radiologische Prüfung
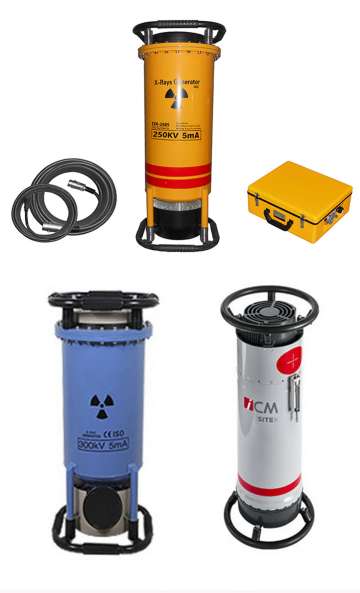
Die Informationen zur Radiographie werden in diesem Artikel nur bereitgestellt, um das Bild der ZfP-Methoden zur Prüfung von Schweißnähten ziemlich vollständig zu machen. Obwohl dieses Verfahren sehr genau ist, ist seine Anwendung eher begrenzt, da es die Verwendung von Gammastrahlen und Röntgenstrahlen beinhaltet, die eine hohe Durchdringungsfähigkeit aufweisen, die es ihnen ermöglicht, durch Metall zu gelangen und Defekte auf dem fotografischen Film zu fixieren. Dies führt zu einer erhöhten Gefahr für die menschliche Gesundheit. Darüber hinaus sind Geräte dieses Typs ziemlich teuer. Daher ist die Verwendung dieser Art von Prüfung sehr spezifisch und erfordert die Verwendung spezieller Schutzmethoden und die Schaffung geeigneter Laborbedingungen für Prüfungen.
Daher haben wir die wichtigsten Methoden zur zerstörungsfreien Prüfung von Schweißverbindungen betrachtet. Es ist offensichtlich, dass die genauesten Testergebnisse und sicheren Bedingungen für ihre Implementierung durch die kombinierte Verwendung von Ultraschall-, Wirbelstrom- und Magnetpartikel-Prüfmethoden bereitgestellt werden.