The ETS2-77 is intended for the mechanized inspection of rails and switches as well as confirmation of the results of a grinding application. The device is capable of testing a wide range of rail profiles.
Application
- possibility to control the rail track and the track switch;
- selective control of the separate rail track areas;
- post grinding machines control;
- all main rail profiles control Р50, Р60, 49E1, UIC 60 and others.
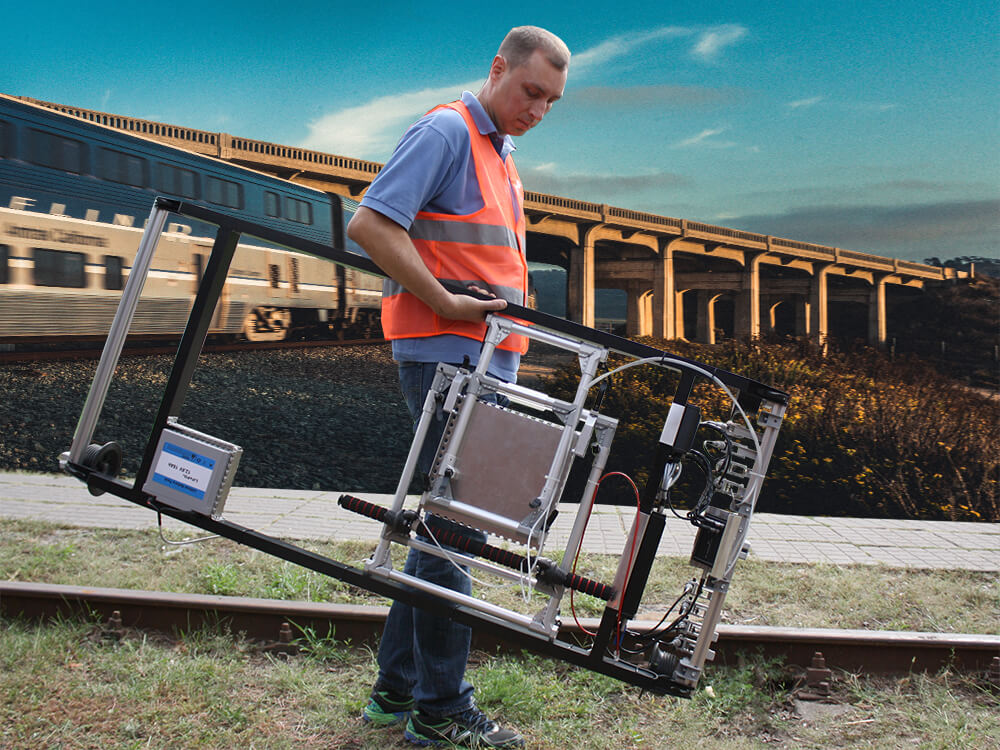
Lightweight and compact
Weight of the assembled flaw detector does not exceed 23 kg (50 lbs).
Overall dimensions of the assembled flaw detector are not more than:
- width - 900 mm
- length - 1730 mm
- height - 350 mm
The ETS2-77 flaw detector is a folding structure, which can be transported as it is a assembled in stowed position.
Main Components
- Aluminium base frame
- Eddycon D - multichannel eddy current flaw detector
- Scanning modules with eddy current probes (ECP)
- Laptop
- Software for test data input, storage and processing
- Reference block
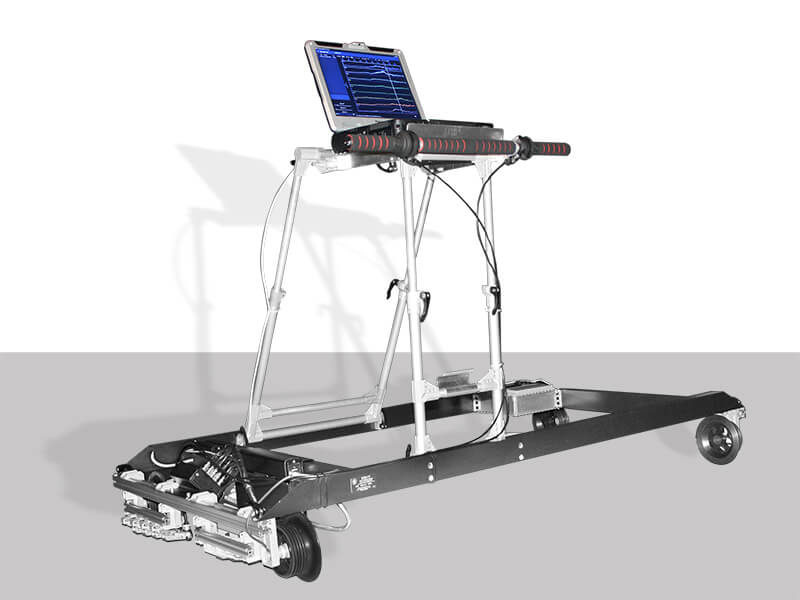
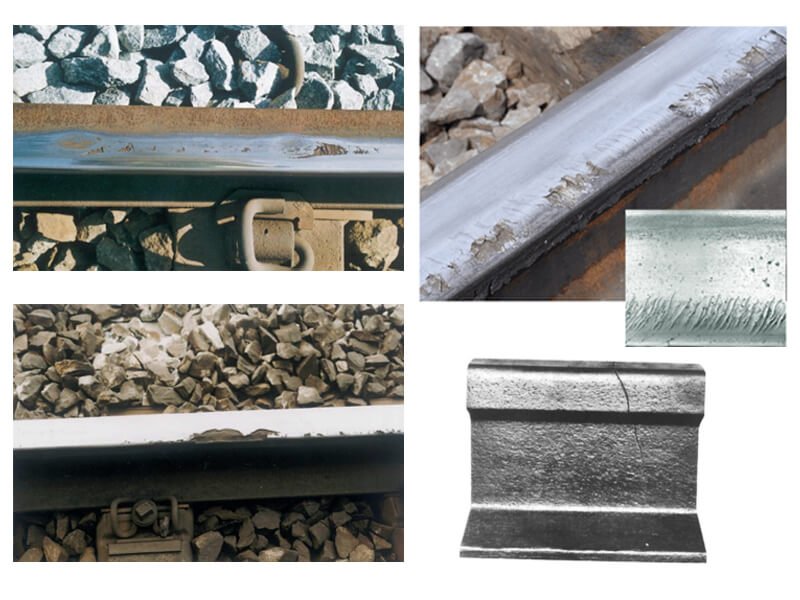
ETS2-77 intended use
The ETS2-77 is intended for the mechanized inspection of rails and switches as well as confirmation of the results of a grinding application. The device is capable of testing a wide range of rail profiles.
The eddy current technology enables localizing the following surface defects:
- progressive transverse cracking (International Defect Code (UIC) 211);
- fissuring /scaling at the gauge corner (International Defect Code (UIC) 2223);
- shelling of the gauge corner (International Defect Code (UIC) 2222);
- wheel burn (International Defect Code (UIC) 225).
The eddy current rail inspection equipment ETS2-77 is capable of evaluating the vertical depth of the defect, thus allowing a more efficient management of rail defects. The inspector can easily decide on the defect removal method: grinding, milling or re-railing, which saves time and money.
ETS2-77 flaw detector advantages
- light aluminum frame;
- specialized abrasion-resistant ECPs allow to evaluate the oblique cracks with up to 3 mm vertical damage depth;
- 8 ECPs application allows to perform the control of the whole head rail surface in one run;
- individual spring-mounted fitting of each ECP;
- fast removal of the scanner during the transfer from one area to another;
- individual adjustment of ECP position;
- operating time – not less than 8 hours;
- specialized SW for setting up, testing and inspection results review
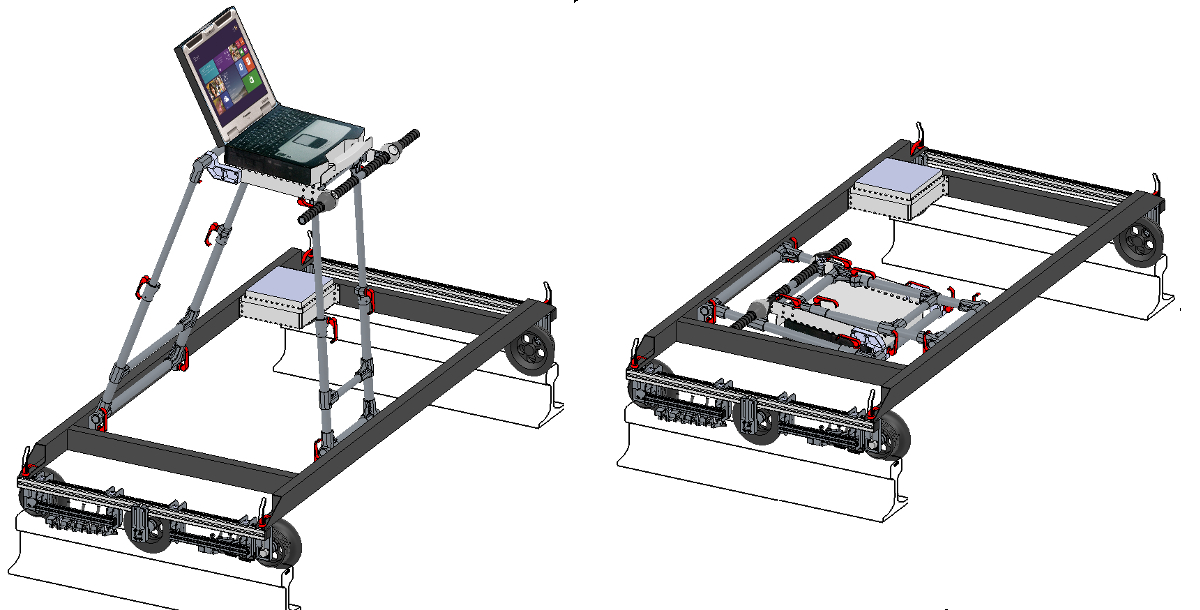
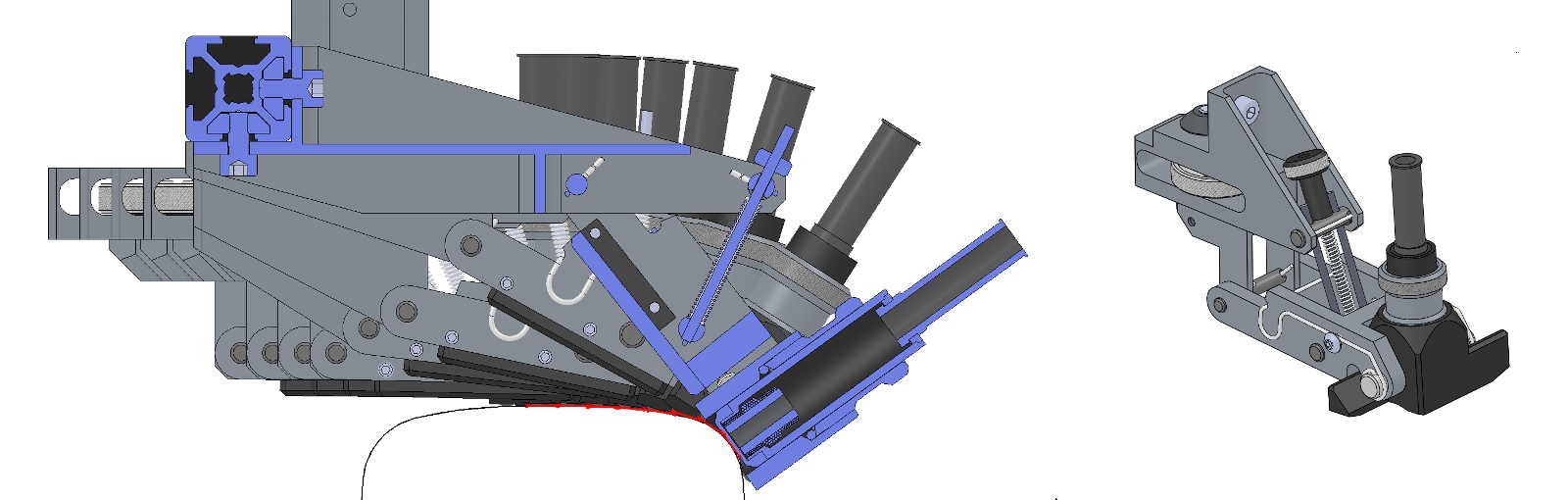
Program for setting up the EC channel
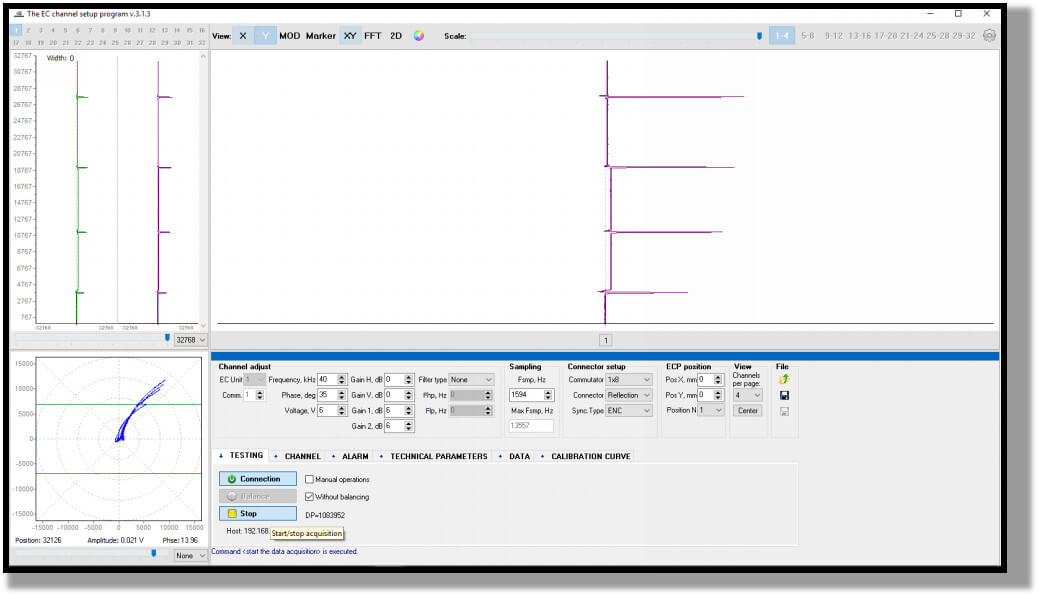
- Quick set up of all EC channel parameters – EC probe frequency, drive voltage, gain, filters, threshold level, sync type, etc
- Four independent threshold levels for automated defect triggering (ALARM) for each displayed area
- Saving the testing setups into the PC or tablet’s memory
Program for the testing
- Real-time display of 8 EC probes information
- Recording the testing results into the PC or tablet memory
- Display of different types of information in the signal visualization area
- Re-calculation of the obtained defectograms
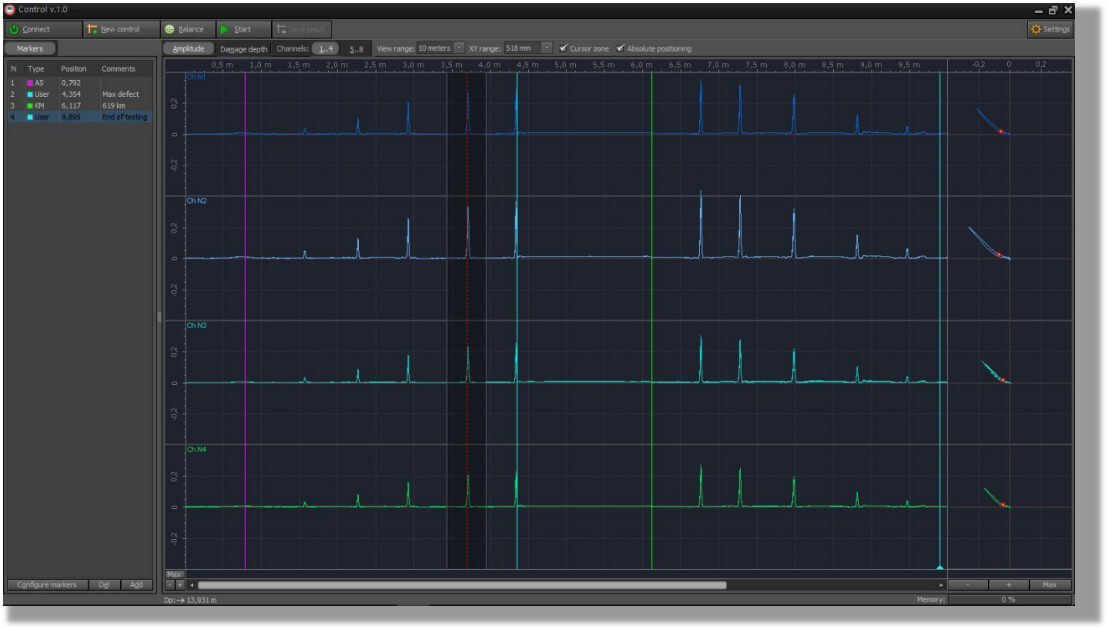
Program for generating the names of railroads
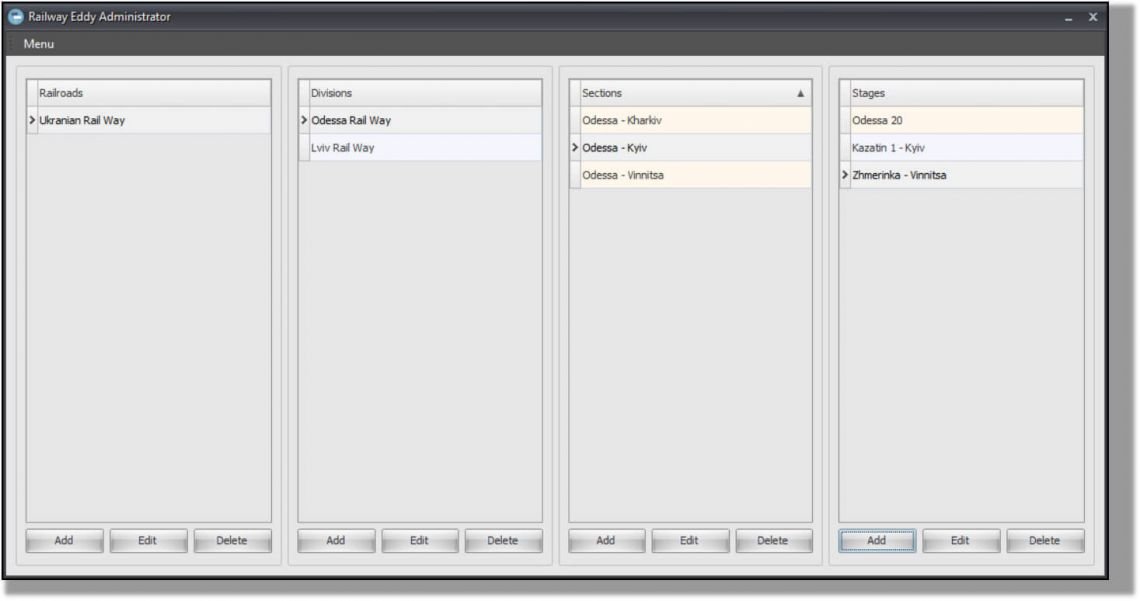
Consists of the following components:
Railroads – Divisions – Sectors – Stages
Program for reviewing the testing results
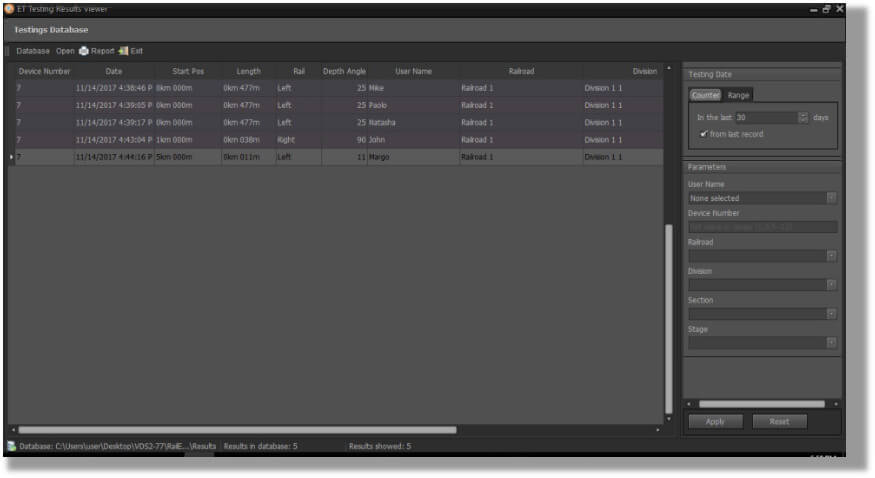
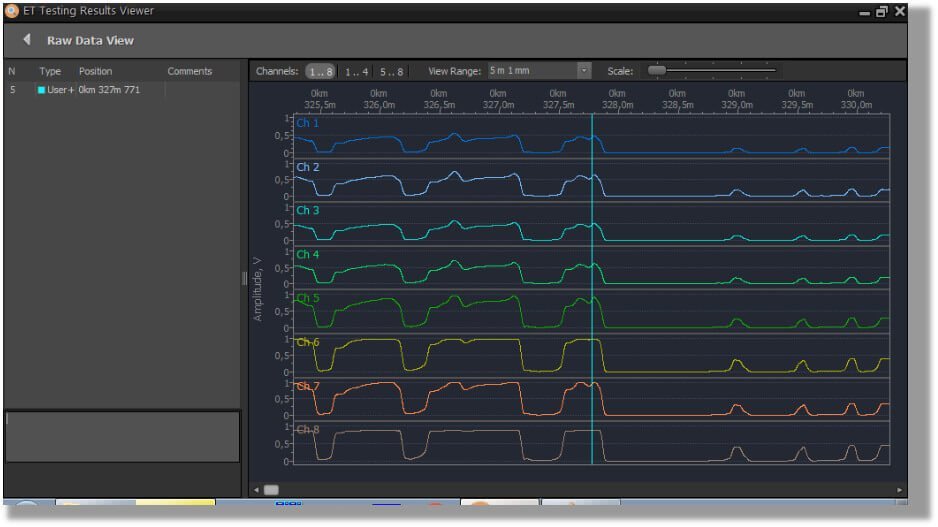
- Reading the test results from the database
- Printing out the test reports
- Archiving the test results
- Reviewing the test results from the remote PC , etc
SPECIFICATION
Model | ETS2-77 |
Flaw detector type | mechanized |
Overall dimensions in the stowed position | 1730 mm × 900 mm × 350 mm |
Eddy current channel | Eddycon D |
Scanning device |
|
ECP quantity | 8 |
Tested area by one ECP | 6 mm |
ECP protection from the abrasion and damage | Ceramic protective cover |
Test velocity | Up to 2 m/s |
Alarm | Visual |
Specialized software |
|
Operating time | 8 hours |
Record and data storage | + PC hard disk |
Working PC | Industrial one, IP rating 65 |
Sollten Sie Fragen haben, wenden Sie sich an uns