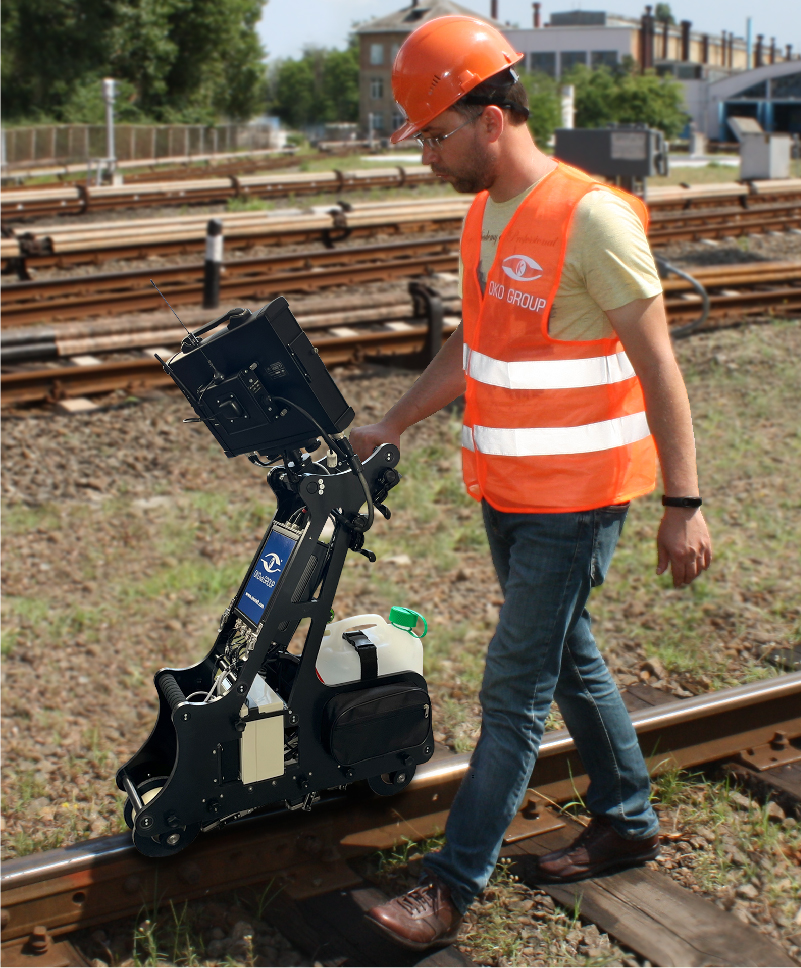
Single-rail inspection trolley UDS2-77
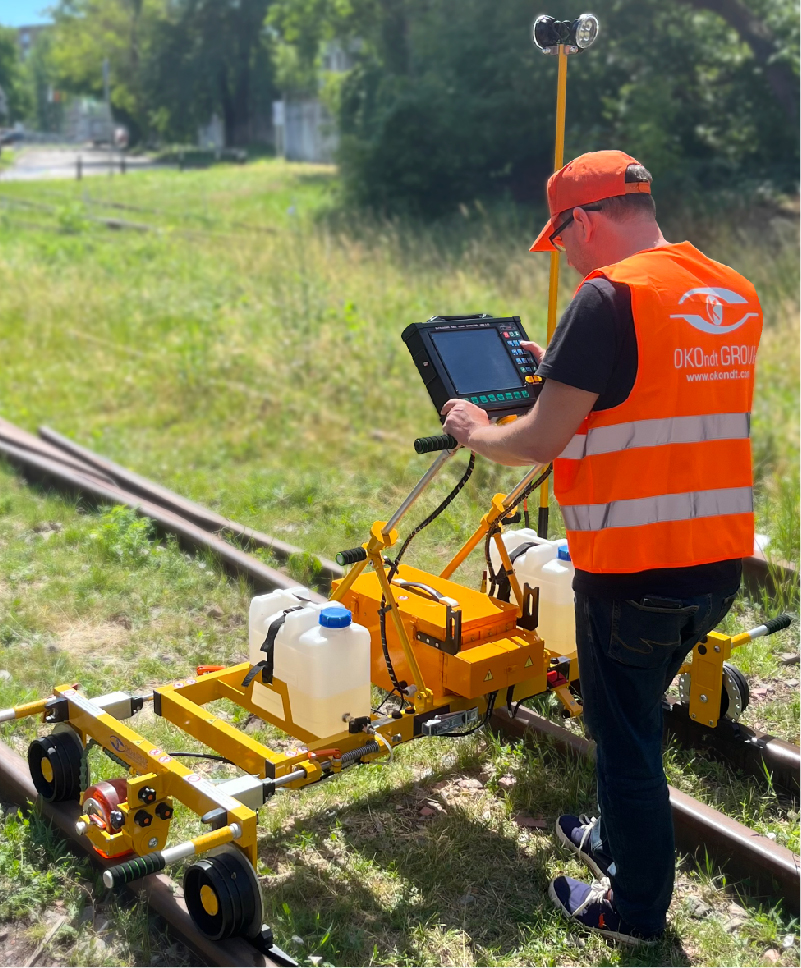
Dual-rail inspection trolley UDS2-73
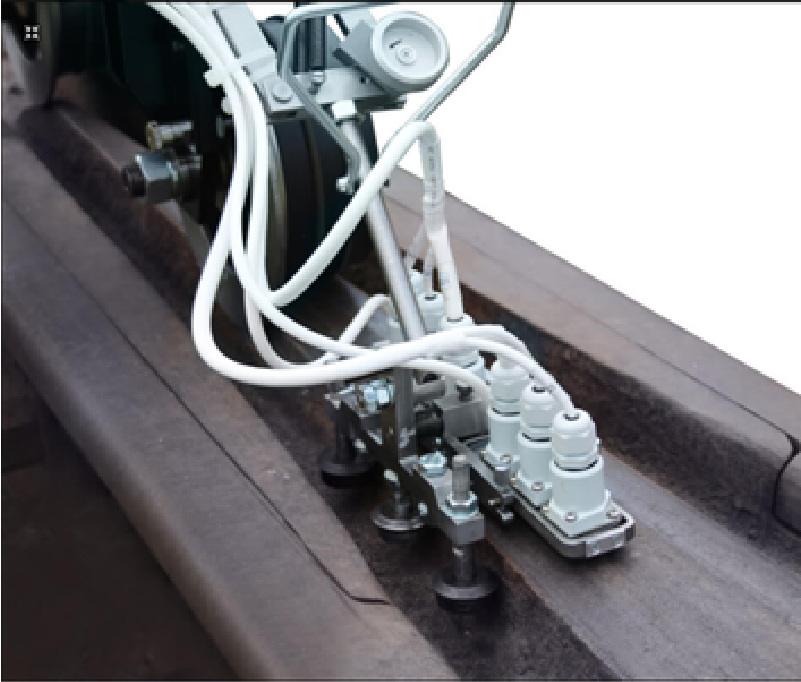
Sliding search system
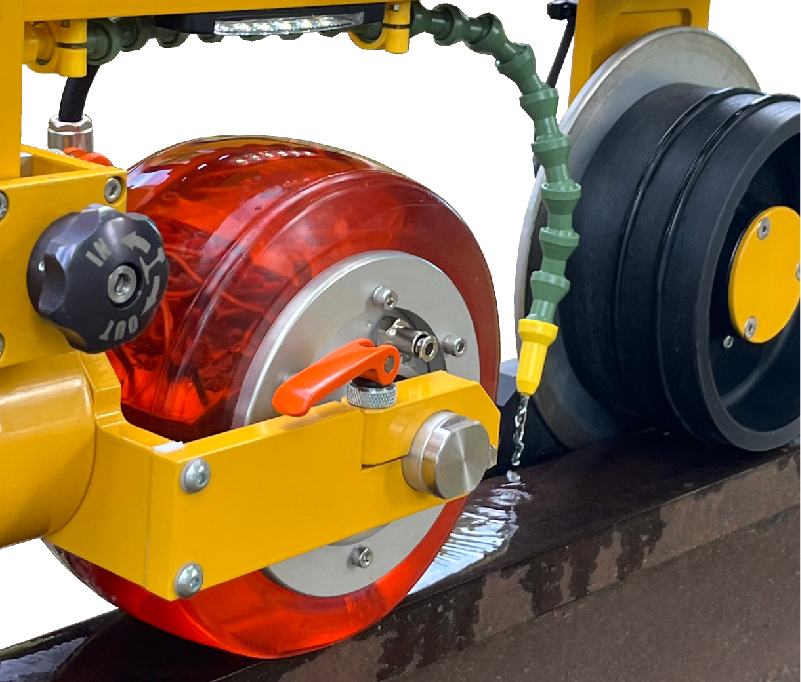
Wheel-type immersion system – «wheel probe»
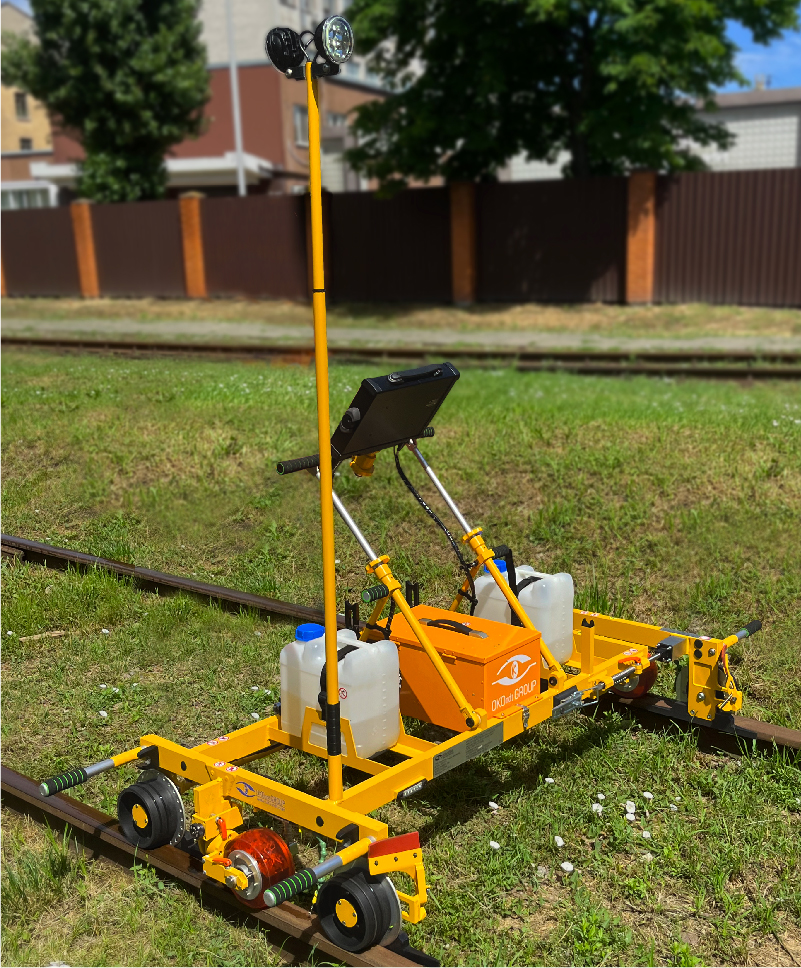
UDS2-73 RSUI inspection trolley with wheel probes and unclenching chassis
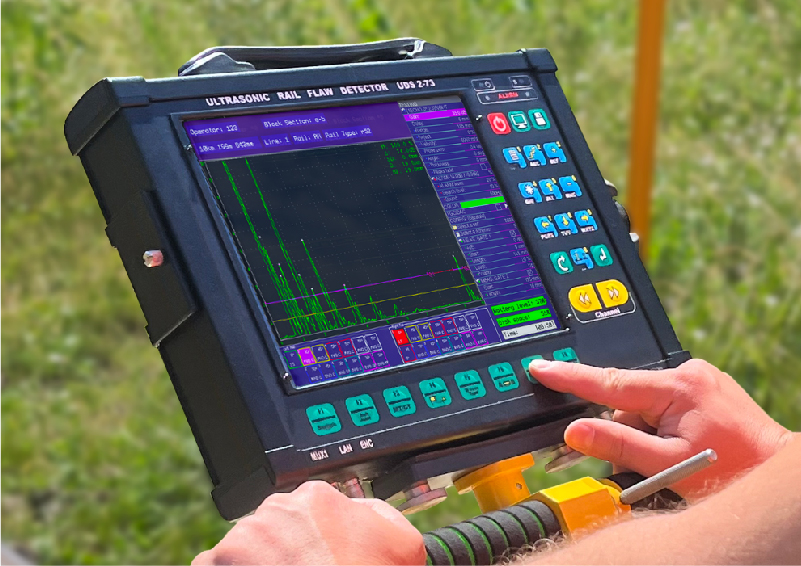
Electronic unit in UDS2-73 RSUI
Hand-pushed ultrasonic rail flaw detectors UDS2-73 and UDS2-77
The middle link in the rail track quality management system (in the part of ultrasonic rail inspection) is the rails ultrasonic testing using hand-pushed ultrasonic rail inspection trolleys, also known as ultrasonic single-rail and dual-rail flaw detectors. This is the most widespread class of equipment used on all railways in the world. Hand-pushed ultrasonic rail inspection trolleys - such as UDS2-73 and UDS2-77 - are used either for confirmatory inspection after high-speed ultrasonic rail devices, or for the main inspection of small track portions, as well as track portions with small radius curves, station tracks and other areas where the use of high-speed means is difficult or ineffective.
Usage of UDS2-73 and UDS2-77 flaw detectors
Hand-pushed ultrasonic rail inspection trolleys are either single-rail (for example UDS2-77) or dual-rail (UDS2-73). Single-rail flaw detectors are most convenient for confirmatory inspection of single defects, while requiring only one operator, who can quickly remove the inspection trolley from the track on his own in the case of train approaching. Dual-rail flaw detectors are more convenient for continuous inspection of small sections of the track.
Search systems of the UDS family inspection trolleys
These types of inspection trolleys can use both sliding search systems and wheel-type immersion systems - so-called "ultrasonic wheels" or "wheel probes".
Each of the search systems has its advantages and disadvantages. The main advantage of sliding systems is auto-positioning of ultrasonic probes on the rail surface, which ensures high stability of the testing sensitivity regardless of the inclination of the inspection trolley (for single-rail flaw detectors), as well as the absence of the need to adjust the inclination of the probes. The disadvantage of sliding systems is the wear of ultrasonic probes, and therefore the need for their regular replacement and frequent recalibration of the System. Accordingly, the advantage of the wheel system is the complete absence of wear of the probes (only the ultrasonic wheel tires are subject to periodic replacement). One disadvantage that concerns primarily single-rail flaw detectors is that the inevitable change in the trolley`s inclination during manual driving along the rail leads to noticeable fluctuations in sensitivity when using wheel probes. The dual-rail flaw detector is practically deprived of this disadvantage. Here it is enough to adjust the correct position of the ultrasonic wheels only once and it will automatically stay positioned during inspection. Therefore UDS2-73 RSUI ultrasonic dual-rail wheel inspection trolley has the advantages of almost "eternal" probes and is free from the disadvantage of sensitivity instability when performing inspection. Let us now consider the capabilities of this trolley in details.
The UDS2-73 RSUI provides continuous ultrasonic rail inspection according to such standards as EN 16729, AREMA, etc. The inspection trolley has push-out chassis, which ensures distinct positioning of the ultrasonic wheels, and is also equipped with entry bars for unhindered passage through switches and frogs. The flaw detector has a large (10-inch) high-contrast display, a convenient, intuitive interface and an ergonomic design. The inspection speed can reach 5 km/h while the sounding is carried out with a step of no more than 1.5 mm along the rail path, which gives a high accuracy of estimating the amplitudes of the detected indications. UDS2-73 RSUI can be used to inspect the rails in tracks with a gauge from 950 to 1676 mm, in other words, all existing tracks.
All the equipment has the level of protection against water and solid particles IP65 and a range of operating temperatures from minus 30 °C to plus 55 °C, so it can be used even in very harsh conditions. Probes and electronics are galvanically isolated from the rails, which allows to significantly reduce the impact of electrical interference.
Testing results display in the flaw detectors of UDS family
The software of the flaw detector allows to view the inspection results in real time in the form of A-Scan, multi-A-Scan, B-Scan for all channels. A special mode with the display of a rail profile helps to intuitively determine location of the detected defects. There is also a mode of simultaneous display of B-Scans for groups of channels by inspection zones: Rail head, Central projection, etc.
During the inspection, the operator can set markers "Crossing", "Bridge", "Bolt hole", etc., which are stored together with the inspection data. UDS2-73 RSUI is equipped with a GPS/GNSS system, so all data is bound not only to the track coordinate, but also to the real geolocation.
The saved data can be viewed directly on the flaw detector as well as be transferred to a PC using a regular USB flash drive.
The PC program supplied with UDS2-73 RSUI provides extensive options for viewing and analyzing of the stored data, as well as generation of a number of reports - for individual detected defects, for inspected areas, the inspection jobs for a certain period, etc.
UDS family PC software development perspectives
In addition, our programmers are currently working on adding a module for intelligent machine analysis of inspection data to this program, which will greatly simplify the work of the testing data analyst. This software module was developed and has already proven itself well in a similar program for high-speed rail testing system OKOSCAN-73HS.
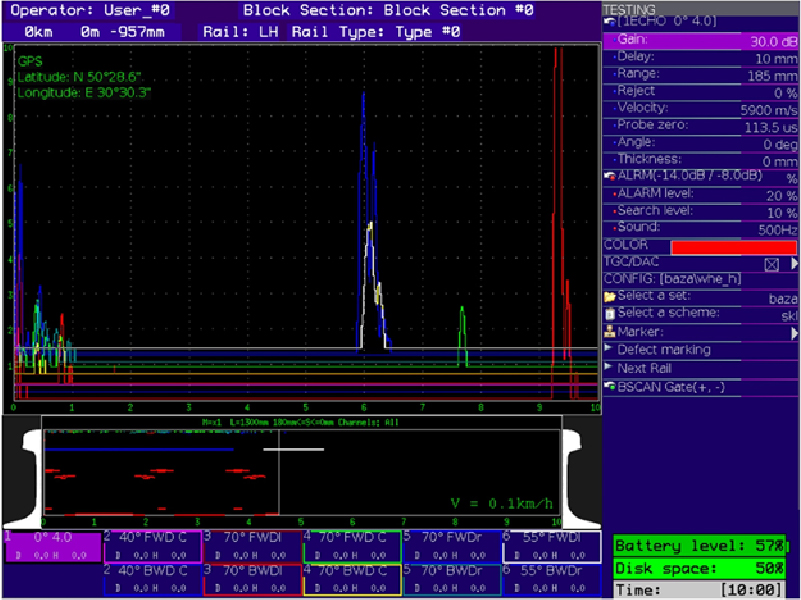
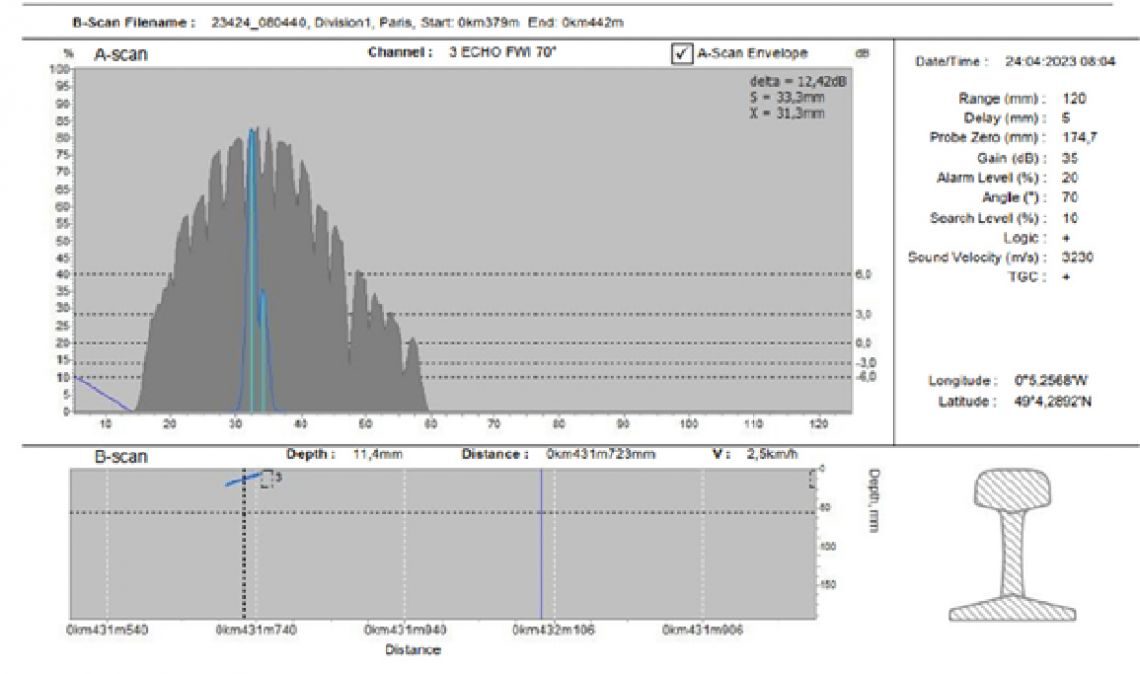