The safety of movement on any railway track in the world depends on the quality of the railway track. The most cost effective solution is following the Risk Based Engineering principles which requires correct and up-to-date information about all rails in the railway tracks. Detection and further monitoring of the technical state of rails with operational defects allow their timely replacement. One of the main components of the rails defects detection approaches is ultrasonic rail inspection, which allows detection of both surface and inner defects in the whole rail cross section (except for the rail base wings).
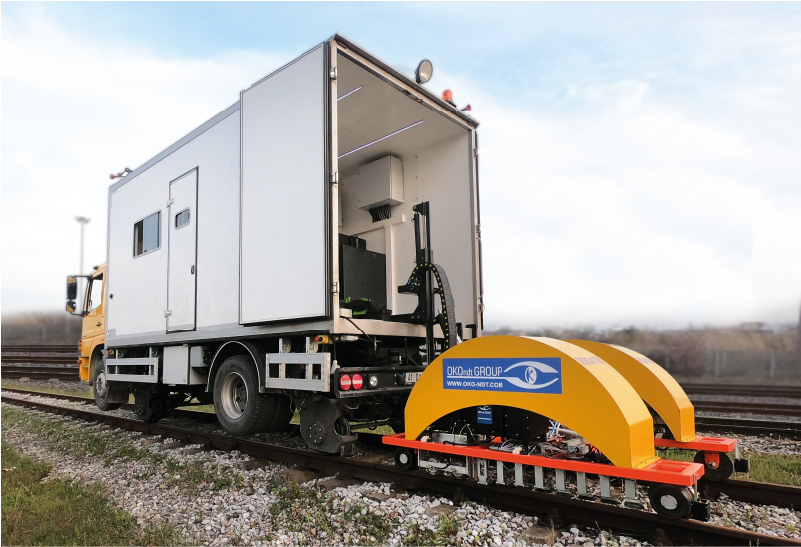
High-speed rail testing system OKOSCAN-73HS UT&ET

Hand-pushed ultrasonic dual-rail inspection trolley UDS2-73 RSUI
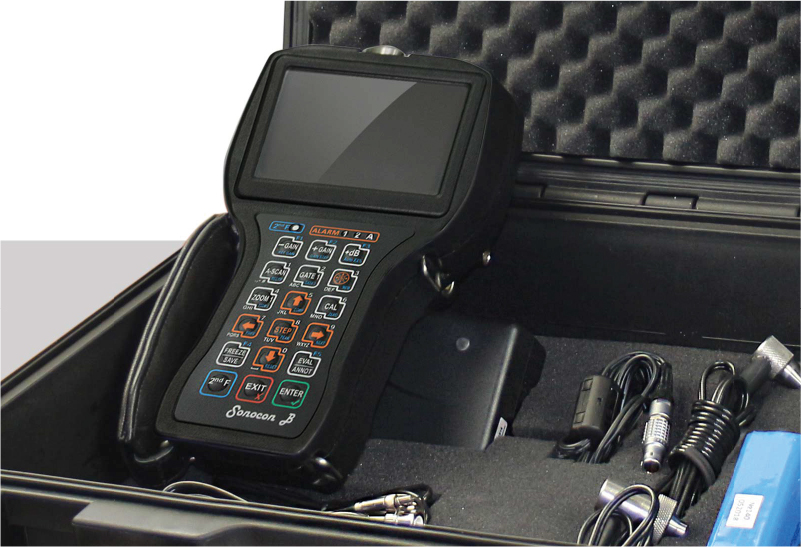
Portable flaw detector for confirmatory inspection Sonocon B
The ultrasonic inspection is usually carried out in three stages:
- High-speed rail inspection using hi-rail vehicles, motorized rail cars, and usual railway cars allows quick inspection of long track distances ensuring detection of all dangerous defects. The test results acquired by such systems are passed to the regional rails UT inspectors for suspect indications confirmation and then can be imported to some central Railway Infrastructure database providing prompt information about the current technical state of each and any railway track portion.
- Inspection using hand-pushed single-rail and dual-rail flaw detectors is carried out for confirmatory testing of the defected areas that were detected during high-speed rail inspection as well as regular inspection of small areas and areas with big quantity of small radius curves, switches, etc. The test results received with hand-pushed trolleys are of the similar type as the high-speed system ones and so can be easily compared with them and exported to the same Central Database.
- In-depth manual inspection of the detected defects that were discovered at the previous stages (when necessary) using manual flaw detectors. Manual ultrasonic testing is also used for both acceptance and maintenance tests of the aluminothermic rails welds.
Building of the integral rails quality monitoring system using all three levels of ultrasonic testing means helps to make the railway operation safer and its maintenance more cost effective.